5 assumptions that can lead to the Valley of Death in laser integration
- Mark Turner and Tony Smith
- May 19, 2023
- 4 min read
Updated: Feb 25

The Valley of Death is a term often used by Silicon Valley insiders to describe the daunting challenges they encounter. It represents a critical phase where limited funding can impede progress, making it crucial to overcome obstacles and prove a concept before launching a product or securing additional resources. Unfortunately, many innovators face delays and misallocations of resources due to shortcuts or unchecked assumptions.
When it comes to laser technology, making wrong choices can have serious consequences, potentially derailing a company's go-to-market strategy and causing significant setbacks in manufacturing, resulting in wasted time and money.
Working alongside our trusted partner Owens Design, we've seen many customers veer off course and travel down paths that ultimately lead to failure. It's important to note that a large percentage of these failures could have been avoided if they had addressed critical assumptions more carefully.
While we have encountered countless unchecked assumptions that could jeopardize a project, we have identified four common assumptions that are particularly detrimental for laser integration projects:
Assumption 1: Integrating laser process into a tool is relatively straightforward
Many people mistakenly believe that building a laser tool or integrating an existing laser into a system is a straightforward task. However, this overlooks the complexity inherent in laser processes. Successful laser integration requires a deep understanding of laser-material interaction, precision motion, metrology, CAD CAM, and debris handling. Oversimplifying the process is a serious mistake that often leads to failure and disappointment.
Assumption 2:
You can treat laser projects like any other automation project
Another common assumption is that laser projects can be approached in the same way as other automation tasks. However, lasers have unique challenges and requirements that require a more methodical and scientific approach. To ensure a robust laser process that effectively works with automation, it's vital to embrace a comprehensive and meticulous strategy. Most importantly, understanding the way the process will work when moving from laboratory testing to actual manufacturing equipment is crucial. Determining process windows is a great way to mitigate this risk.
Assumption 3:
The hardware setup from the manufacturer’s lab test is the optimal choice
Many people assume that the hardware setup used at a laser applications lab at the time of the feasibility study is a “golden template”. However, blindly adopting these setups without further evaluation or customization is a mistake. It's crucial to recognize that the manufacturer’s laser labs often handle a wide range of applications, leading to quick and convenient setups. Challenging this assumption and diligently determining the truly optimal setup for specific project requirements is vital for successful laser integration and maximizing ROI.
Assumption 4:
The automation PLC team can easily manage the integration of laser process software
Another prevalent assumption is that the same team responsible for integrating other automation components can seamlessly integrate the software part of a laser process. However, laser integration poses unique challenges due to the intricate CAD CAM operations and algorithms involved, especially in precision laser processing and micromachining. Assuming that integrating laser process software can be approached with the same ease as other automation components often lead to major delays, blown budgets and undesirable results. Working with a partner that already has relevant software products is critical to success.
Fostering effective communication and collaboration early on in the project between the process, the automation and the business teams is crucial.
Assumption 5:
The process and automation teams collaborate solely during machine prototype phase
To avoid unnecessary delays and to ultimately save time, the process and automation teams should work side by side early on – even at the process specification phase. Fostering effective communication and collaboration early on in the project between the process, the automation and the business teams is crucial. A collaborative process will yield a much more desirable result than the traditional waterfall process. This will ultimately save time and money.
So, how can we avoid the perils of the Valley of Death in laser integration? It all starts with taking a methodical approach instead of rushing in headfirst. We have witnessed many people diving into projects at full speed while neglecting careful consideration. They make hasty changes along the way, ultimately leading to failure and finding themselves in the Valley of Death. We strongly recommend consulting with trustworthy experts who have years of experience in the field. By clearly defining the path, and thoroughly considering project requirements, the chances of successfully navigating the project and avoiding pitfalls are significantly increased.
In summary, by dispelling common assumptions, adopting a methodical and collaborative approach, and seeking expert guidance, companies can navigate the Valley of Death in laser integration. Embracing this holistic strategy that balances risk, schedule, and capital investment sets the foundation for successful laser integration.
If you’re looking to get the right tool for the job, the endless options (such as choosing the right laser) in the market can be daunting. Our 360-Mastery Methodology, a process unique to TLS, was built to help you choose a hardware configuration that’s optimal for your application. By thoroughly understanding your needs, providing a technology roadmap including systematic design-of-experiments crafted for your needs, our experts can take you from research, through experimentation to manufacturing success — avoiding development-pitfalls and saving you business time and resources.
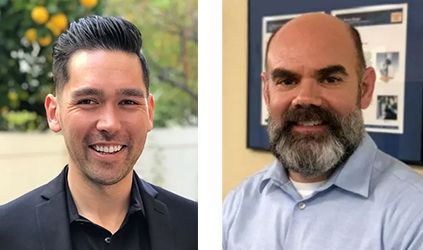
About the authors
Mark Turner, CEO of Turner Laser Systems
Comments